
IBM Watson IOT
Cognitive Visual Inspection
IBM Visual Insights uses cognitive capabilities to review and analyze parts, components, and products and identify defects by matching patterns to images of defects that it has previously analyzed and classified. Create hundreds to thousands of defect models using cognitive and human expertise. Deploy models to edge computing on production lines to facilitate rapid image capture by camera and cognitive identification of defects. Quickly assess quality inspection metrics across manufacturing processes. Cognitive capabilities can help reduce inspection times, increase yield, and facilitate continuous process improvement.
Project Duration - One month
Collaborator - Weina Chai & Linan Dong
Project Type - Internship project
AS-IS Scenario


May is a line inspector, her responsibility is real-timely check every object defect report took by the station camera, and she will manually confirm the defects by reviewing the photo and report.
She sometimes change the defect types, but If she found some defects she cannot identify, for re-confirmation, she will pass to another inspection team, and they will identify these images separately and make decisions.
In the factory she stay, 366’000 photo needed to be examined every day, only counted on 90 inspectors.
It’s time consuming to keep training new inspectors. Joe also wants to reduce the inspection time to reduce the production cost. Currently, a production cycle takes 8 days, his team need 0.5 days to do the inspection, it will be a huge cost saving even if he can reduce 1% inspection time.
To Joe, May is not the only case quit her job by accident. He manages 6 inspection groups, 90 inspectors. Everyday he comes to the factory, the first thing is ensuring his inspectors are stay on their spots properly.
May was weary to do day to day shift job and the monotonous but stressful job, she wants to quit. She speaks to her supervisor, Joe.
AS-IS Pain Points
-
The inspection process takes too long.Total production cycle needs 8 days, 0.5 day is for 5 inspection procedures. Each stations need 20mins manual inspection time. If total inspection time reduces from 0.5 day to 0.3 day, it will increase 3-4% productivity.
-
All counts on human’s experience to inspect.Regard to the high inspector withdrawal rate, and reduce the training efforts, using small team to manage the inspection work.
-
Manually configure the reason behind the defects data.Count on expertise’s experiences to figure out the reason and solution behind abnormal defects.
Project Goals
-
Automate inspection processes, accurately identifying defects with confidence and speed, and significantly reducing the need for manual inspections.
-
Using cognitive classification and comparison, including confidence thresholds, provide more consistent and accurate product inspections compared to manual methods.
-
Centrally monitor visual inspection processes throughout a manufacture organization.
-
Increase speed and accuracy of defect identification to help reduce inspection time, improve manufacturing yield, and increase process throughput.

Stakeholder Map

TO-BE Scenario

Since IBM COVIA joined in, May no longer need to do the regular defect inspections, COVIA covers that.
All May need to do is verifying each of the defect image one by one. And she will be able to manually correct the result.
Joe will teach COVIA to recognize these unexpected defects by tagging. Most of time he feels like he is a teacher.
With IBM COVIA’s help, the inspection time reduced over 80%, his team helps total shipping time reduced to 4%, which means his team save a lot of money for the company.
Joe no longer need to wait for his crew submit the report and he manually calculate the inspection efficiency. Now he can simply ask COVIA to show the real time statics anytime.
Joe feels happy now, not only his crew as stable than before, but he can use 1/3 team to manage the same inspection workload.
TO-BE Scenario Process & Hills


HILL1
Bob, model manager, can monitor all models’ accuracy in production environment, and increase the accuracy by updating the model with new defect images collected by COVIA automatically, without inspection team’s help.

Dashboard Screen

HILL2
May, Inspector, will be able to reduce her inspection time and increase accuracy by reviewing the COVIA inspection result, instead of record manually

VIQ Screen

HILL3
Joe no longer need to wait for his crew submit the report and he manually calculate the inspection efficiency. Now he can simply ask COVIA to show the real time statics anytime.

3D Model Screen
DESING PROCESS

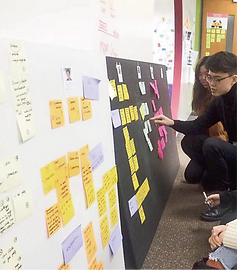
CARD SORTING
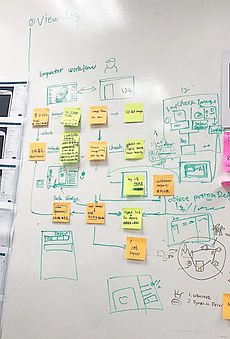
WORLFLOW

lO-FI PROTOTYPE
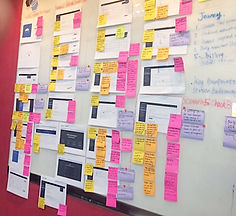
HI-FI MODIFICATION

Dashboard Screen
Inspection Supervisor can click each of the KPI cards to view the corresponding trend, and the detail defect ranking list.